ITB’s Merah-Putih Catalyst Tested at Pertamina’s Dumai II Oil Refinery
By Adi Permana
Editor Adi Permana
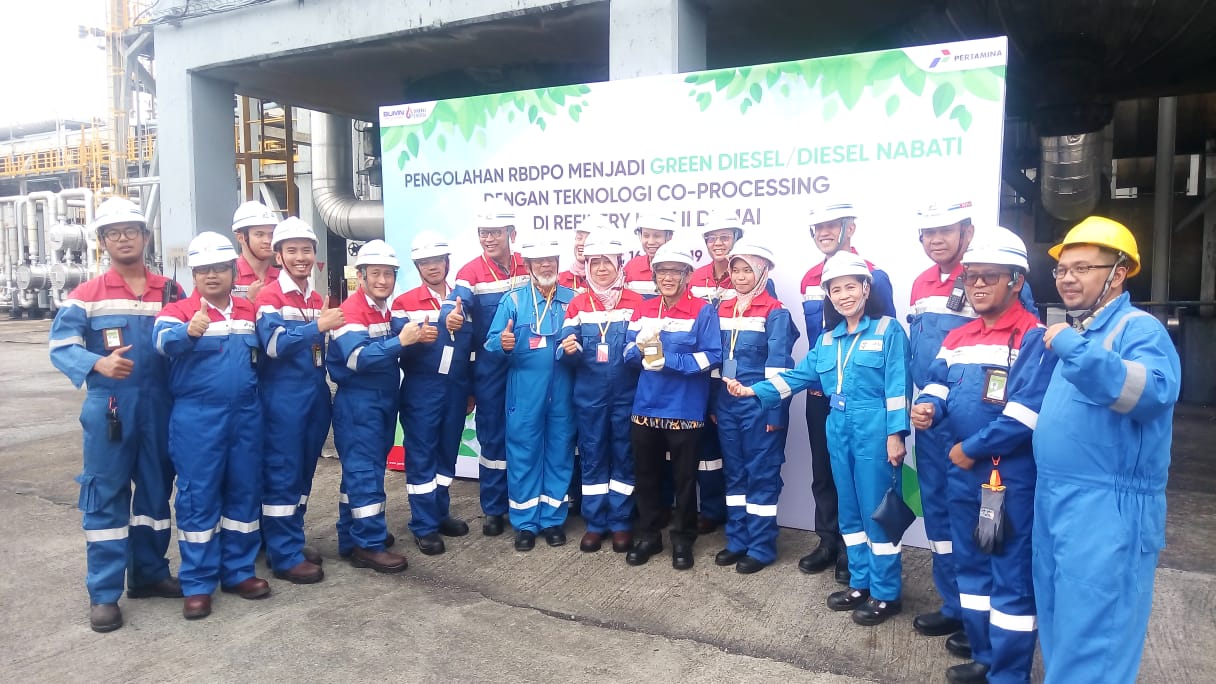
BANDUNG, itb.ac.id – Catalyst created by research team from Institut Teknologi Bandung (ITB) and Research and Technology Centre (RTC) of Pertamina underwent commercial-scale testing. The test this time is conducted at Pertamina’s RU II Dumai Oil Refinery to generate LCGO (Light Cycle Gas Oil made from fossil fuel), palm oil into diesel, and green diesel using co-processing method.
On Thursday (16/5/2019), Minister of Research, Technology, and Higher Education (Menristekdikti) Prof. Mohammad Nasir visited the oil refinery. He was accompanied by Rector of ITB Prof. Dr. Ir. Kadarsah Suryadi, DEA., Pertamina’s Director of Investment Planning and Risk Management Heru Setiawan, and General Manager of Pertamina RU II Nandang Kurnaedi, as well as several invited guests from various ministries and institutions.
The visitation aims to see the success of co-processing of green diesel made from palm oil which is conducted by RU II Dumai using the catalyst developed by Laboratory of Chemical Reaction and Catalysis (TRKK) of ITB and Pertamina. Co-processing is a fuel processing that use mixture of fossil fuel and green diesel materials.
Catalyst research team from ITB were present during both the loading process, start up and lab test. Among the members of the research team are Dr. Carolus Borromeus Rasrendra ST.,MT., Dr.Ir. I.G.B. Ngurah Makertihartha, Prof.Dr.Ir. Subagjo (team leader), and Dr.Ir. Melia Laniwati Gunawan MS.
On an interview, Dr. Melia Laniwati said that the tested catalyst (entered) into the reactor were about 12 tons. With several consideration such as unit condition, the test were not conducted 100% using palm oil, but mixed with fossil fuel (LCGO). This process is called co-processing.
“The first developed catalyst was tested on December 2014. That time, we still see drawbacks. Hence, it is fixed/enhanced to make the second generation. When the opportunity came when it was time for the reactor to change its catalysts, in 2019 the catalyst is used,” explained Melia.
The test result is satisfying. The quality of mixture between diesel and green diesel is very favorable and fulfill market specification. “So we can ensure that the co-processing test was successful,” she said. For that success, the team from ITB hope Pertamina can apply the catalyst to similar reactors on other oil refineries, because material substitution can save country’s foreign exchange reserves.
Catalyst is a chemical material used in oil processing. Research and development to formula, characterization and performance test of Merah Putih Catalyst on laboratory-scale is done at TRKK Laboratory of Faculty of Industrial Technology (FTI) ITB, while the pilot scale at RTC Pertamina and industry scale test was done at Pertamina’s oil refinery.
TRKK laboratory, collaborated with Research Technology Center (RTC) Pertamina, have created various hydrotreating catalyst. Since 2011, no less than 150 tons of hydrotreating catalyst have been produced and used on 8 reactors at five Pertamina’s oil refineries.
The first generation catalyst has been developed since 2010, while the development of second generation catalyst began in 2015. The second generation catalyst, with trademark PK 220 HBD, has been tested in pilot reactor at RTC Pertamina for more than 10 months.
Cited from pertamina.com, Nandang Kurnia explained that the development of the catalyst has been conducted from 2008 until the birth of second generation catalyst which optimally has been a supporting element of co-processing at RU II oil refinery. All process in the development of the catalyst were conducted by the nation’s best human resources and tested at Pertamina’s Oil Refinery.
After successfully created catalyst, CPO processing is conducted at Distillate Hydrotreating Unit (DHDT) facility at Pertamina’s Dumai oil refinery, with a capacity of 12.6 MBSD (Million Barrels of Steam per Day). The shift between the old and the new catalyst was done on February 2019. The injection of green fuel materials was done on March 2019.
Menristekdikti, Prof. Mohamad Nasir explained that the use of 10%-12% feed of green fuel can save nation’s cost for importing crude oil by up to 1.6 million USD a year. He also hopes this program can be continuously developed so that the utilization of green fuel at Pertamina’s oil refinery rises.
“With utilization of just 10%, the country could save so much. In the future hopefully the number rises,” said Nasir.