Ahmad Fauzi: Research Corrosion Resistance of Ti-Al Intermetallic Alloy At High Temperature.
By Teguh Yassi Akasyah
Editor Teguh Yassi Akasyah
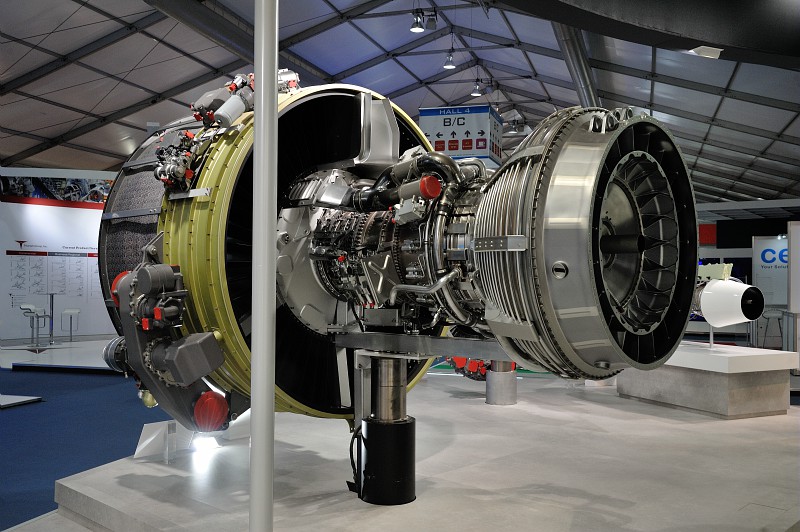
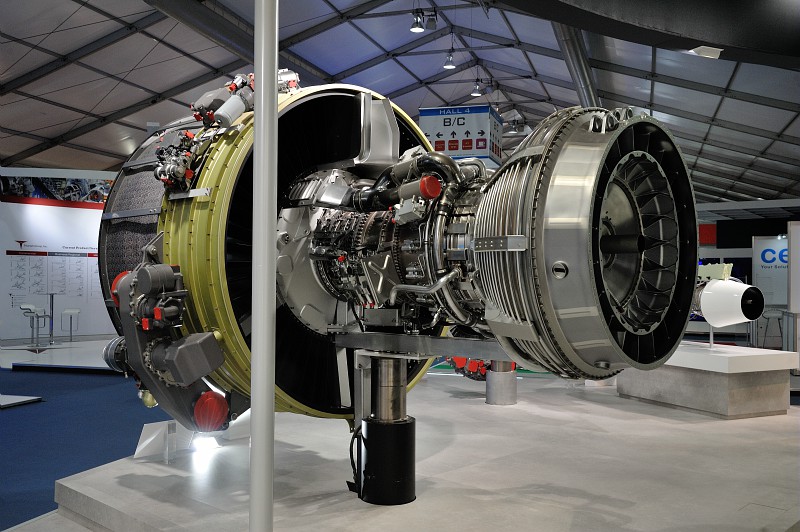
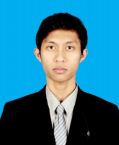
Research On Corrosion Resistance Against Ti-Al Intermetallic Alloys
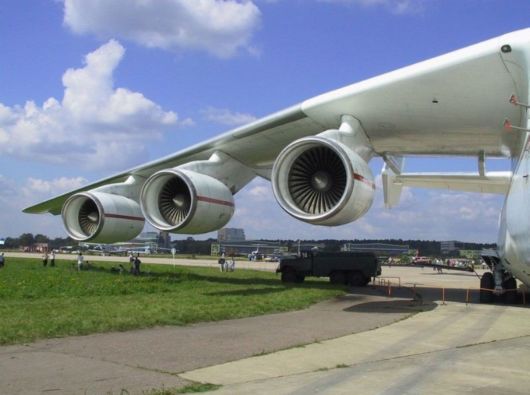
In this study, Fauzi tried to research the corrosion resistance of the alloy by using pack aluminizing and hot corrosion test. Pack aluminizing is a method of enrichment of Al in the alloy with a diffusion coating process, which uses a source of Al coatings by the method of pack cementation. It can be selected to increase the levels of Al on the surface of a two-phase alloy-Ti3Al alpha / gamma-TiAl substrate in order to maintain sufficient mechanical properties at high temperatures. In this study, the material used to pack aluminizing form NH4Cl as activator, powder of Al and inert filler Al2O3 with the composition of each of 2%, 20% and 78%. This process will produce a phase TiAl3 which rich on its Al at the surface of the substrate.
While the hot corrosion tests performed on both the in-alloy and alloy coatings that are not in-coating at a temperature of 700 C, 800 C and 900 C with a temperature variation test of time ie, 1, 5, 10 and 22 hours. Temperature variation performed to study the resistance of the alloy at various temperatures. Testing is done by dipping the alloy in molten salt 90% Na2SO4 and 10% NaCl. Through these tests can be seen corrosion rate based on changes in weight and depth of corrosion.
Based on the research, the results of the experiment showed that in the alloy coating by pack aluminizing provide better corrosion resistance in corrosion rate is parabolic. Alloys that are not in-coating showed significant exfoliation especially at a temperature of 800 C and 900 C. As for the hot corrosion test, at a temperature of 800 C obtained the highest corrosion rate based on changes in weight and depth of corrosion. In addition to testing the robustness, Fauzi also test XRD and SEM / EDS to determine the composition of the oxides are formed.
Ahmad Fauzi: Academic and Organizations Must be Balanced
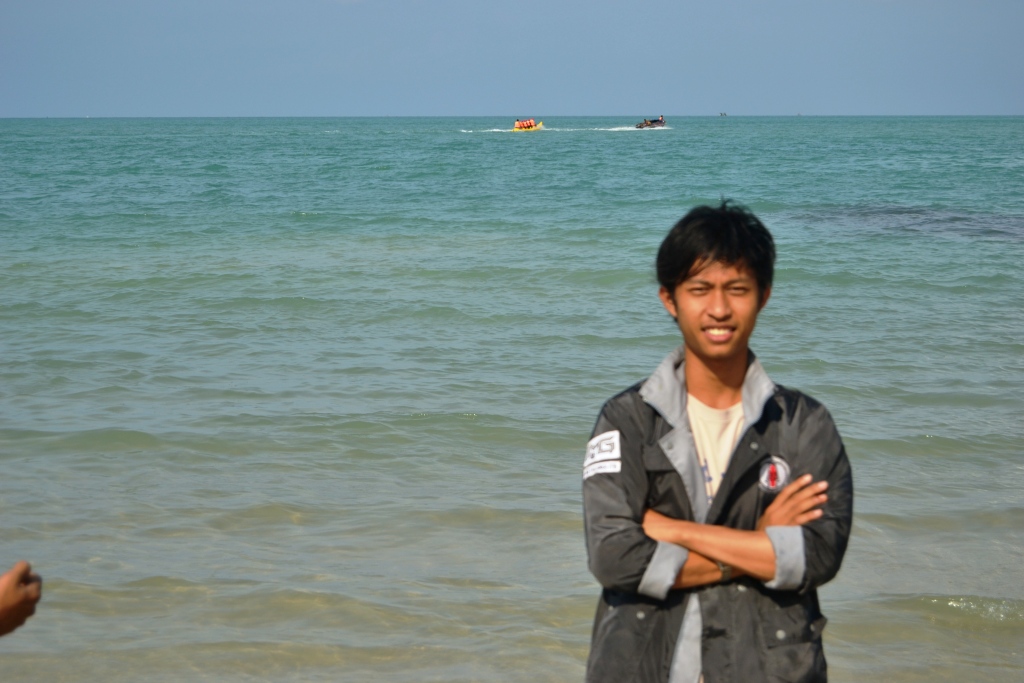